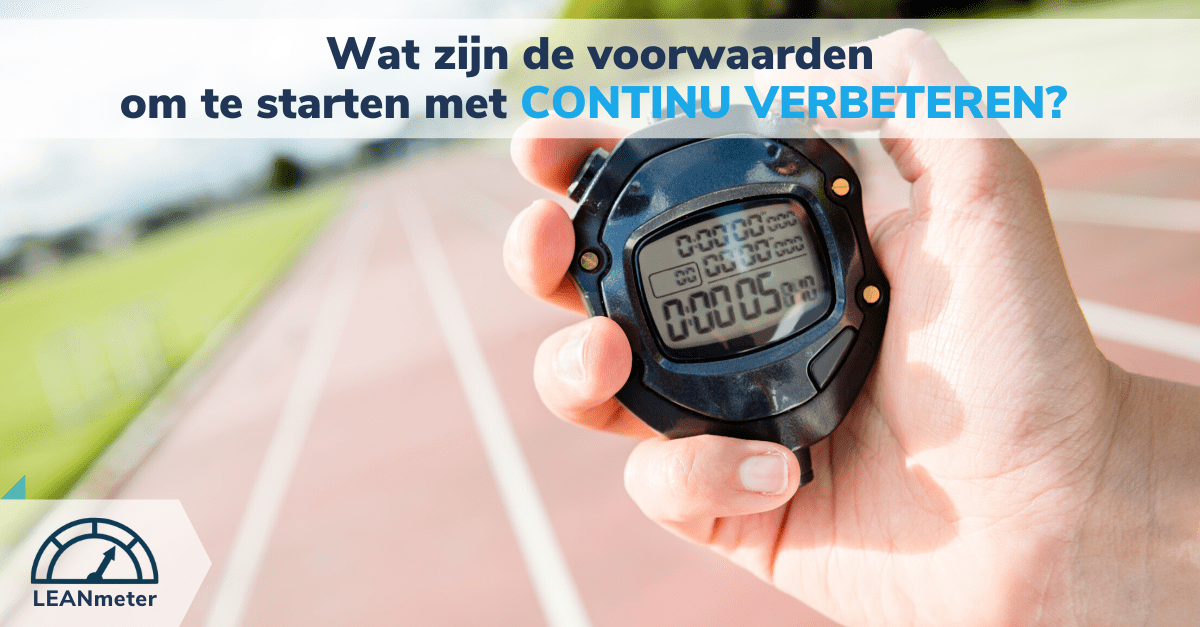
There are roughly two ways to achieve improvement in your work: with small steps or through a major change all at once. In crisis situations or with major innovations (such as a new product line or change in strategy), it is usually better to implement the change all at once, project by project. In all other situations, it is always necessary to monitor quality, efficiency or working conditions and, where necessary, improve them step by step. Essential is that everyone is involved, can take initiative and actively participates in the changes. Always central to this are the questions of why the change is needed and what it contributes to the goals set. If the answer is not clear, there is often a different cause under the problem than initially thought. By looking for the causes, you prevent solutions from being suboptimal and creating more problems than solutions.
How do you start with continuous improvement?
Do you recognize yourself in any of these examples?
“I work at an organization that supports companies in absence management, among other things. I support company doctors and labor experts and have a lot of contact with our clients. I am often the first point of contact and therefore the business card of our company. New clients join us regularly. The first impression they get of us is important. I always make sure they receive a flower as a welcome. In a consultation between different branches I explained how we do this. It turned out that this did not happen at all of our branches, but everyone was enthusiastic. It has now been implemented in all branches.”
“I work at a large brewery. We stand for high quality, so we always sell fresh products. Because we don’t always manage to sell the entire stock because demand fluctuates, stock has to be destroyed regularly. Recently, the cost of dumping the products has increased significantly. I suggested that we systematically examine how to address the landfill costs. So not coming up with solutions right away, but looking at the causes first. After we had done this, two directions for solutions emerged: first, preventing the creation of residual products. This required the various departments involved to work better together. Second, we changed the allocation of costs so that departments that have an impact on costs are also responsible for them, thus encouraging them to “pollute” as little as possible. The result is that the costs of disposing of residual batches are more manageable.”
“I work at a housing cooperative with mostly social housing. There is increasing demand for these homes, but housing needs are also changing, so supply and demand are increasingly diverging. I am experiencing an increasing workload because we are not working as efficiently. I brought this up in the team meeting and suggested we look together to see what we can do better. At first my colleagues were not so enthusiastic, because everyone is already so busy. I then, together with a blackbelt in our organization, figured out for one of the work processes how much time we could save if we did it smarter. The result made my colleagues enthusiastic. We implemented the improvements and are now tackling the processes one by one. The workload has been reduced and job satisfaction has increased.”
Do you know if you are starting continuous improvement the right way?
The LEANmeter gives insight in how Lean you are already working. You see your strong points and get advice for improvement, individually and as a team.
Complete the LEANmeter and get the right impulse, it only takes 5 minutes of your time.
Leave A Comment
You must be logged in to post a comment.